How to Create Tabby Shell Stucco
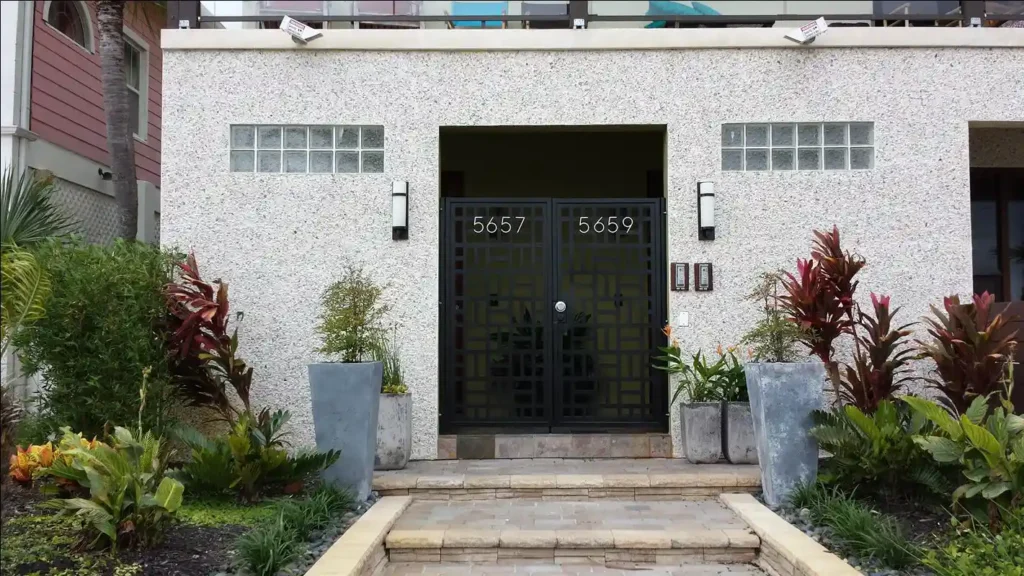
History:
Original Tabby Shell Stucco was made from a mix of slurry of water, homemade lime, local sand, and oyster shells. Occasionally, aggregates of broken glass, brick or other similar products were added. The mixture was poured into a wooden forms or rectangular bottomless cradles made of finished boards approximately two inches thick. The length of the cradle varied; the height was 20 to 22 inches in the eighteenth century but was reduced to 10 to 12 inches in the nineteenth century to minimize collapse and provide greater strength. The sides were held in place by dovetailed braces. The tabby was tamped and leveled by hand.
Round pins set at regular intervals held the cradle in place during the entire process. The tabby air-dried in its cradle for two to three days. After it hardened, the form and pins were removed and placed atop the first pour or “round” for subsequent rounds, thus building a wall in a layer-like fashion. The finished wall was then brushed with a broom before stucco or whitewash was applied.
Minute modifications to this procedure distinguish Tabby Revival tabby from its copied original. In addition to the commercially available Portland cement and lime altering the mix after 1880, the cradle was modified to eliminate the use of pins: huge clamps now held the sides. The qualities of the cement enabled builders to discard the previously essential stucco.
The sand was always from a local body of water. Sand from salt water was washed to remove as much salt as possible, since salt causes decay and deterioration, such as spalling. Oyster shells, procured from Indian middens or trash piles, provided a well-washed aggregate and, when burned, produced the third ingredient, lime. A “rick”, or bonfire, was built, starting with a frame of hardwood tree trunks surrounding a deep pit filled with pine knots. Layers of logs and oyster shells were then piled on top and set afire. The intense fire burned the shells, turning them into a white powder called quicklime, which reacted with water to set or cure the mixture. After 1880, this burn was omitted in favor of purchasing pre-bagged lime and Portland cement.
Tabby Shell Stucco making was labor-intensive and dependent on weather. February through September were the recommended months for making Tabby. This allowed builders to avoid winter freeze-thaw cycles and rainy, hurricane-prone autumn months, and take advantage of months of high humidity, which shortened the setting time. Drying tabby was protected from rain by palmetto branches. With the introduction of Portland cement set times decreased however, tabby builders heeded this traditional advice, but may not have always needed to follow it.
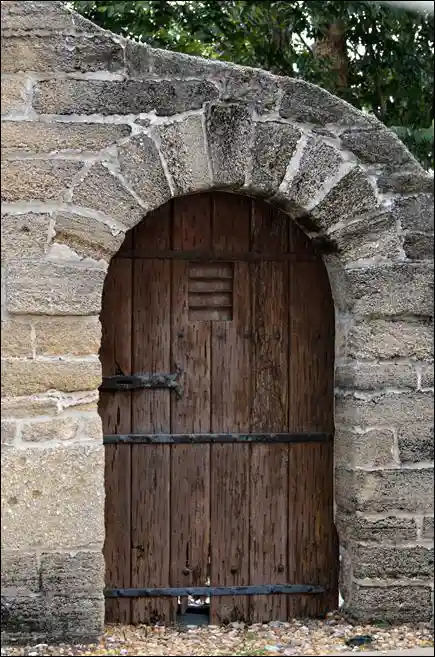
Modern Tabby:
Today, buildings are rarely constructed with Tabby Shell Stucco unless historic re-construction is necessary. The shell finish, however, has come back in style: all over the U.S. Tabby stucco is an art. However, without the proper manpower and equipment, the finish could easily become an expensive disaster.
Begin by preparing the wall using the traditional method of moisture barriers, lath, link etc… whichever is correct for the substrate. Apply base coat and scratch coat as required.
Before applying the finish coat, create sifting boxes out of hardware cloth and 2’x4’s and elevate them near a water source. The wire gauge will vary depending on what size shell is desired. Spread about a 1” layer of shell in the sifting boxes. Use a spray nozzle on a garden hose to pass a constant stream of water over the shell as the boxes are shaken back and forth vigorously. Rake the shell with the back of a steel rake as it is being shaken. This process is absolutely necessary to remove as much of the fines as possible.
Lay Masonite or plywood under the wall to catch the shell that does not stick so it may be washed and re-used. Mix the finish coat a little rich and apply over the scratch coat. While applying the finish, have someone cast the shell into the wet mud. Make sure the arm strokes are consistent. It is best to have the same person cast the shell on each wall so if a slight pattern emerges, it will be consistent. The very best way to apply the shell is with a pneumatic gun. While the shell is being cast into the wall, have someone pat the shell in place with a soft float. This will seat the shell in the finish coat. Wait until the finish coat starts to ridge (you shouldn’t be able to pull the shell off the wall easily) and knock the shell down with a soft float.
Continue wetting the wall down for the next few days as is normally done with a traditional stucco finish. It is important to seal the finished product after waiting at least one week (refer to sealer instructions for details).
By using this method, a Tabby Shell Stucco finished look will be achieved without the use of actual Tabby building material. Tabby building material has a multitude of issues and does not withstand the elements well. It crumbles easily and has terrible moisture issues. By simply applying the shell to the exterior of a properly stuccoed surface, the historic beauty may be appreciated without the historic issues.
Traditional Tabby:
For a more traditional Tabby Shell Stucco look follow these instructions.
Begin by preparing the wall using the traditional method of moisture barriers, lath, link etc… whichever is correct for the substrate. Apply base coat and scratch coat as required.
Make the Tabby Shell Stucco topcoat using Oyster Shells. In a concrete mixer, mix 1 part lime, 2 parts cement and 3 parts sand. Mix thoroughly for at least 20 minutes gradually adding just enough water to make a thick, mortar mix. Then add the oyster shells towards the end of the mixing. Keep adding them until you see the Shell distributed consistently in the stucco. (The closest Shell we carry to Oyster Shell is our Coastal Shell, it has Oyster Shell in it but is not pure Oyster Shell.)
Apply a layer of the tabby stucco to the walls, using a trowel. The layer should be about as thick as the oyster shells. Apply firm pressure. Start from the bottom and work your way up. Once finished, mist the stucco occasionally over the course of 5 to 7 days this will help the Stucco cure.